As a company that focusing on researching vacuum die-casting technology, this article will give you a further in-depth understanding of vacuum die-casting technology, including an overview of vacuum die-casting, the advantages of vacuum die-casting, and the production process.
Overview of vacuum casting
Casting is a manufacturing process in which liquid material is poured into a mold and make it to solidify. Vacuum casting uses a vacuum to remove air from the mold, helping to ensure that the object takes on the desired shape.This process be used to casting plastic and rubber parts usually.At the same time,vacuum casting also be used for rapid prototype or small-scale process because it can more cheep and more efficient than injection mold.
Advantages of vacuum casting
The main advantage of vacuum casting is that it allows for high accuracy and repeatability, making it an perfect choice for those process need precise dimensions.It also allows for more complicated designs to be cast that making it has a wide range of usage in the industry.IN industry,vacuum casting often be used to low-volume production of prototypes,this process has more advantage compared with traditional injection.However, vacuum casting is not suitable for all applications. For example, it cannot be used to cast materials that are sensitive to heat or pressure.
Low cost is another advantage for vacuum casting.vacuum casting is more cheep than other rapid prototype process such as CNC.Because worker only speed less hours can make a mold, which can be reused multiple times.however,CNC machining need more expensive tools and materials.
The products made by vacuum casting with excellent dimensional accuracy.Those parts can fit together perfectly without needing other processing steps such as sanding or drilling.
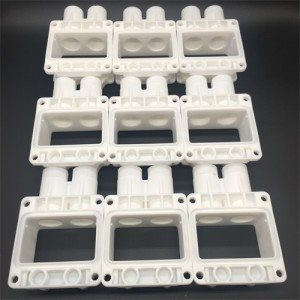
Vacuum casting allow people to complex designs that’s because the mold of vacuum casting all made by 3D printing technology.As a result,parts that would be make impossible to made by other process can be easily made by vacuum casting.
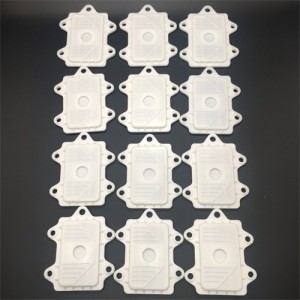
Worker will made a Exquisite mold by 3D printing technology.Past,people used to using CNC technology to make molds,but now additive manufacturing can do the job quickly.with advent of 3D printing technology,pattern maker ‘role become more and more important,On the other hand, the master mold be made by 3D printing can be directly used without any further modification.
After master mold finish,worker will suspend it in casting box and poured liquid silicone around it.The molten silicone is allowed to cure inside the casting box and keep it’ temperature is 40℃ about 8-16hours.when it solidified and curing is completed,the mold will be cut open and take out the master mold and leaving a hollow which has the Same size as mold.
Third step:Producing the parts
The hollow mould be filled with PU by funnel,To achieve uniform distribution and to prevent any air bubbles from forming. then seal the mould in casting box keep around 70°C to cure.when it cool down,removed it from the mold, and other processed as necessary.this process can be repeated 10 to 20 times mostly.if Going beyond the limits will cause the mould lose its shape and affecting dimensional accuracy.
Vacuum casting is a versatile and relatively quick process that can create small batches of detailed parts. It is ideal for prototypes, functional models, and marketing purposes such as exhibition pieces or sales samples.Do you have any upcoming projects for vacuum cast parts? If you need this technology to help you,please contact us!
article source: https://www.chinaruicheng.com/news/vacuum-casting-process-steps/
Media Contact
Company Name: Xiamen Ruicheng Industrial Design Co., Ltd.
Email: Send Email
Country: China
Website: https://www.chinaruicheng.com/